About Alcast Company
About Alcast Company
Blog Article
The 9-Minute Rule for Alcast Company
Table of ContentsA Biased View of Alcast CompanyNot known Details About Alcast Company Alcast Company Can Be Fun For EveryoneThe Ultimate Guide To Alcast CompanyThe 8-Minute Rule for Alcast CompanyAlcast Company Fundamentals Explained
The refined distinction hinges on the chemical content. Chemical Comparison of Cast Light weight aluminum Alloys Silicon advertises castability by minimizing the alloy's melting temperature level and boosting fluidness throughout casting. It plays a critical role in allowing complex molds to be filled up precisely. Furthermore, silicon adds to the alloy's toughness and put on resistance, making it beneficial in applications where longevity is important, such as vehicle components and engine parts.It likewise enhances the machinability of the alloy, making it easier to refine into finished items. In this means, iron contributes to the total workability of light weight aluminum alloys.
Manganese adds to the strength of light weight aluminum alloys and enhances workability (Foundry). It is frequently made use of in functioned light weight aluminum products like sheets, extrusions, and accounts. The presence of manganese help in the alloy's formability and resistance to cracking throughout manufacture procedures. Magnesium is a light-weight element that provides toughness and impact resistance to light weight aluminum alloys.
Our Alcast Company Ideas
It allows the production of light-weight parts with exceptional mechanical properties. Zinc enhances the castability of aluminum alloys and assists control the solidification process throughout spreading. It improves the alloy's stamina and solidity. It is frequently found in applications where complex forms and great details are needed, such as attractive spreadings and certain automobile parts.
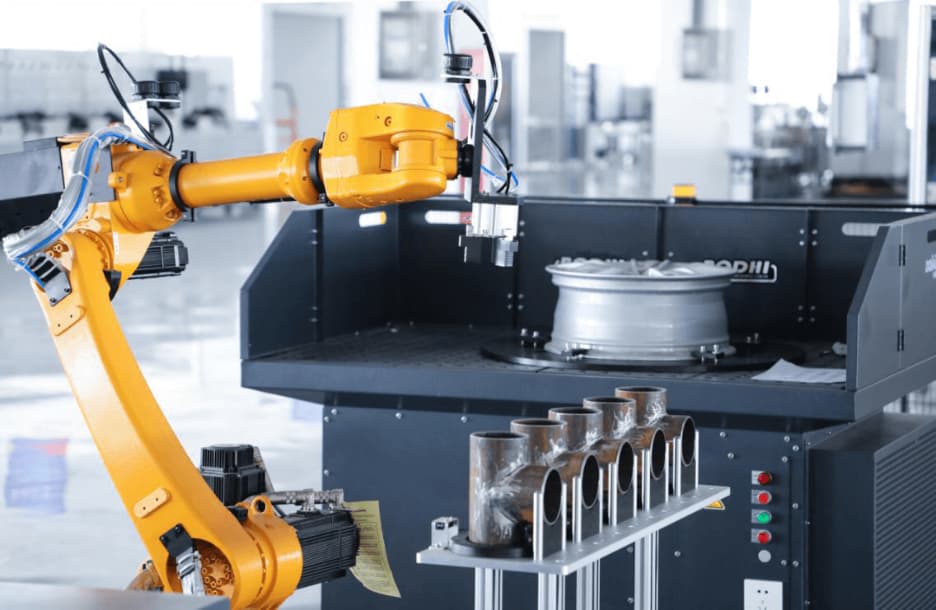
The primary thermal conductivity, tensile strength, return strength, and elongation vary. Amongst the above alloys, A356 has the highest possible thermal conductivity, and A380 and ADC12 have the most affordable.
The Ultimate Guide To Alcast Company
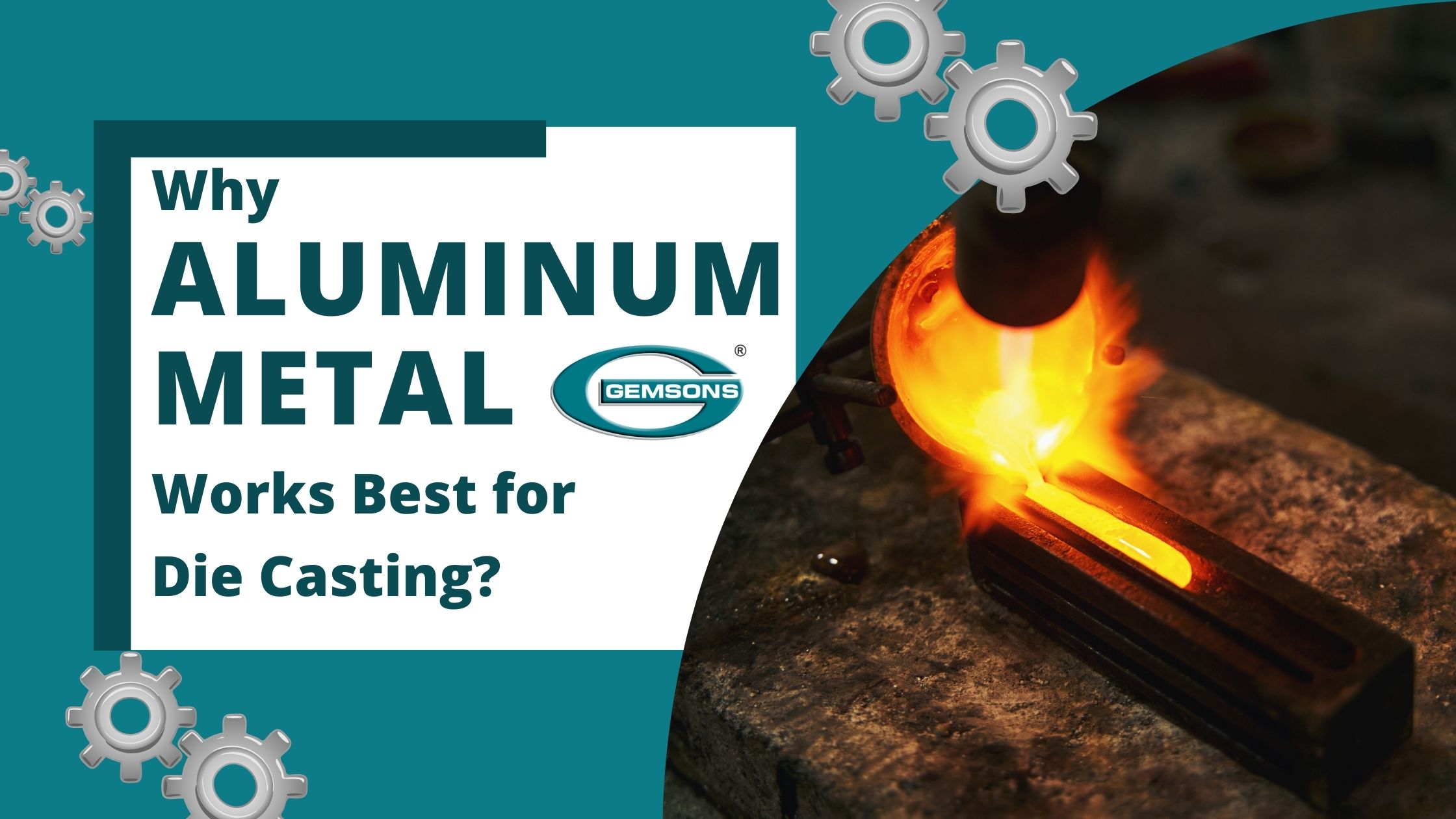
In precision spreading, 6063 is fit for applications where detailed geometries and top notch surface coatings are critical. Instances consist of telecommunication rooms, where the alloy's premium formability permits smooth and cosmetically pleasing designs while preserving architectural honesty. In the Lighting Solutions industry, precision-cast 6063 components produce sophisticated and effective lights fixtures that call for elaborate forms and great thermal efficiency.
It brings about a better surface coating and far better deterioration resistance in A360. The A360 exhibits superior elongation, making it suitable for facility and thin-walled parts. In accuracy spreading applications, A360 is fit for sectors such as Customer Electronics, Telecommunication, and Power Tools. Its enhanced fluidity permits detailed, high-precision parts like smart device coverings and interaction tool real estates.
The smart Trick of Alcast Company That Nobody is Discussing
Its one-of-a-kind buildings make A360 a beneficial option for accuracy spreading in these sectors, enhancing item resilience and high quality. Aluminum Castings. Aluminum alloy 380, or A380, is a widely used casting alloy with a number of distinctive qualities.
In accuracy spreading, light weight aluminum 413 beams in the Customer Electronics and Power Tools sectors. This alloy's premium deterioration resistance makes it an exceptional choice for exterior applications, making certain resilient, durable items in the mentioned industries.
Alcast Company for Beginners
The aluminum alloy you select will considerably influence both the casting process and the properties of the final product. Since of this, you need to make your choice meticulously and take an informed approach.
Establishing the most suitable aluminum alloy for your application will certainly suggest considering a large selection of characteristics. The initial classification addresses alloy qualities that affect the manufacturing procedure.
The 8-Second Trick For Alcast Company
The alloy you choose for die casting directly impacts several facets of the spreading process, like exactly how simple the alloy is to deal with and if it is vulnerable to casting problems. Warm splitting, likewise called solidification fracturing, is a common die spreading defect for light weight aluminum alloys that can lead to interior or surface-level rips or cracks.
Particular light weight aluminum alloys are more vulnerable to warm cracking than others, and your choice must consider this. It can harm both the cast and the die, so you ought to look for alloys with high anti-soldering properties.
Corrosion resistance, which is already a significant feature of light weight aluminum, can vary significantly from alloy to alloy and is a crucial characteristic to consider depending on the environmental conditions your product will be subjected to (Aluminum Castings). Use resistance is one more residential or commercial property typically sought in aluminum items and can set apart some alloys
Report this page